Building Information Modeling (BIM) is a high-technology process transformational method to address project complexity and rapid development. A BIM-based project produces digital assets that transform how supply chain partners work together to improve the design and construction process, enabling early problem identification and removal, generating cost and schedule benefits, and improving the facilities management and operations process after occupancy. Rather than the traditional two-dimensional (2D) process used in facilities design and construction, the BIM delivery method uses three-dimensional (3D) digital models created by architects, engineers, designers, and fabricators (extracting 2D drawings as needed). The 3D models are easier for project stakeholders to comprehend, promoting improved understanding and design collaboration. Technology manufacturers offer BIM software platforms (e.g., AutoDesk, Bentley, Graphisoft, CATIA, and Tekla) that do not always seamlessly share model data, but interchange standard development projects are attempting to address interoperability (e.g., Industry Foundation Class [IFC] standards development sponsored by buildingSMART International).
What Is BIM?
BIM offers advantages in multidisciplinary collaboration, cost and schedule, project understanding, and design constructability. Access to digital models early in and during the design process offers a multidisciplinary view, with higher-order collaboration among project participants and better design understanding through visualization, reducing Requests For Information (RFIs) and field rework. Usually, several BIMs (and sub-BIMs) are created for the project (e.g., by the architect; structural engineer; civil engineer; mechanical, electrical, and plumbing [MEP] engineers). Individual models can be virtually combined at any point in the process to support an enhanced form of digital coordination and design review. The earlier in the process this coordination occurs, the fewer problems emerge.
During the design process, BIM is used to coordinate discipline-specific designs to detect (and rectify) interfering components, using a single combined virtual 3D model. Such coordination is achieved before drawing production, saving time and money and leading to identification of functional design clashes and physical component clashes. Project stakeholders other than design consultants benefit from this process because their ability to inform the design early is greatly enhanced. Because 3D drawings are extracted from BIM, their production can be more cost-efficient, timely, and better quality, with more user-friendly images than 2D and virtual software facility walk-throughs. Experience shows that the capability to visually understand the design more completely at all project stages is one of the greatest BIM process benefits.
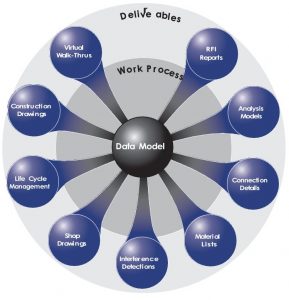
Figure 4.7. BIM Is a Data-Centric Design Process
Improved Consistency and Error Reduction
As a data-centric process, the BIM-based delivery approach uses consistent digital representations of each discipline’s work product or data model to produce many required project deliverables (e.g., drawings, specifications, material quantities, visual design reviews). This new relationship between data and drawings can reduce errors, inconsistencies, and uncertainty in drawings used by each discipline to inform the rest of the project supply chain. BIM provides a visual system representation and also a robust selection of data about each component, addressable by third parties (e.g., material quantity and specification, component location, member forces for connection design). With high levels of sophistication working in the BIM environment, users might work directly from BIM, eliminating the need to produce, review, modify, and distribute shop drawings. BIM is instrumental in reducing errors and RFIs (see Figure 4.7).
Project BIM Coordination, Administration, and Systems Integration
The BIM-based delivery process applies a managed approach to interference detection and change control by developing a comprehensive framework for clash detection and subsequent interference resolution issue management. Most of the commercially available software products that perform this type of interference detection do so programmatically, using model-defined geometry. The interfering components are automatically identified based on criteria set by the user. The design team can innovate more effectively as issues that arose only in the field are now addressed early in the design process, with breakthrough results compared with the traditional process. Successful use of BIM methods depends heavily on managing multiple models for effective allocation. Given current standards for data interoperability among leading 3D vendors, combining 3D models from different systems is key (e.g., solutions using NavisWorks Technology Framework, a managed approach to interference detection and change control; Solibri Model Checker, IFC-based interference detection and reporting on building components by discipline, type, severity, location). Regardless of software, the traditional quality control process is enhanced, not replaced, by programmatically detecting discipline component interferences early and during the design and construction process (with significant return on investment). This new coordination and collaboration process is managed by a new role, a Project Collaboration Administrator (PCA), often known by other names (e.g., BIM model manager, model owner, project BIM coordinator), working under the project manager to collect and process 3D models from participants to improve the model management process and coordination. PCA services scope includes assisting the project manager in collaboration process administration for interference detection and visualization of a single model, with no responsibility to directly modify individual consultant or contractor 3D models (see Figure 4.8).
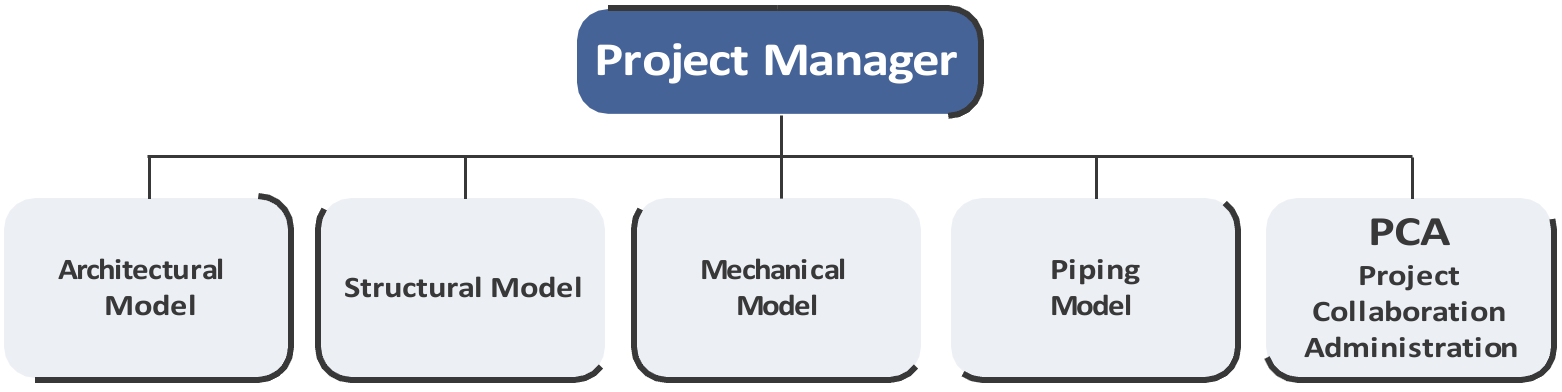
Figure 4.8. Typical Placement for the PCA in the Project Organizational Structure
Simulation-Based Modeling
BIM enables development of 4D models to incorporate time and schedule into existing 3D BIM. Some key attributes associated with these models improve site planning by enabling what-if scenarios to test and improve plans (e.g., simulations of installation conflicts, design clashes, workflow management; construction and schedule sequences; resource space planning scenarios). 4D models typically are used to illustrate construction sequencing activity. The 4D process is straightforward if BIMs are sufficiently granular to link individual (or groups of) elements in discipline BIMs with date-driven construction activities on the contractor construction schedule. This model is played back to visually simulate actual events. Current 4D creation technology (e.g., NavisWorks Timeliner; Synchro) supports many BIM platforms and scheduling platforms (e.g., Microsoft Project, Primavera SureTrack). This improved understanding often facilitates the decision- making required to schedule work in logistically challenging environments.
Facility Management Opportunities
In a BIM-delivered project, underlying digital models allow each component to contain a rich association of data on its attributes (e.g., size, weight, material properties, cost, specifications, assembly diagrams, maintenance procedures, schedules). BIM lays groundwork for derivative facilities management models that can be broadened over time. BIM spatial attributes improve facilities space planning or tenant management, providing fast, accurate, and automated access to area definitions. Early identification of facilities management requirements supports development of specifications and requirements for design and construction models.
A current impediment to full use of BIM for facilities management is the lack of interoperability among BIM platforms (IFC standards can be helpful in overcoming this obstacle). BIMs developed during the project design and construction phases must include the data needed to support useful facilities management operations, requiring substantial cooperation between owner teams and the designers and construction team.
The increased use of BIM in design and construction logically leads to owner demands for BIM facility models that can be used to manage the facility during its life cycle (e.g., at GSA, NIBS model standard committee, Construction Users Roundtable, AIA, U.S. Coast Guard, Veterans Administration, state agencies). Several case studies (e.g., by GSA) have proven the benefits of deploying the BIM approach early in the project, getting consultants and contractors on board, and ensuring clearly defined and understood contract documents and BIM project objectives.
Best Practices in BIM Execution
A number of best practices relate to use of BIM-based delivery. (1) First and foremost, the decision to use BIM practices should be made early in the project, with BIM based on digital models from the civil engineer, architect, structural engineer, MEP, and related subcontractors (and contractor during the design phase).
- BIM-based delivery needs development of contract requirements for specific BIM objectives. The contracts should be developed to include BIM specifications (e.g., terms and specific requirements for production of building information models, technology to be used, disciplines requiring participation, discipline-specific scope of work), using available reference
- Definition of the scope of discipline components to be modeled is key given that effort and cost are associated with these modeling activities. The types of discipline components common in BIMs today include architectural, structural, and MEP BIMs. As the BIM platform becomes more mature and robust with respect to component catalogs and as BIM users become more sophisticated in applying BIM to internal processes, it will become commonplace for disciplines to model more (4) The contracting phase should be devoted to model ownership, specifically the definition of permissible and intended uses for models. (5) A project coordination specification must be explicitly developed to address BIM process coordination and collision detection as well as required reporting; detailed team member processes, roles, and responsibilities; and a process for identifying, communicating, and tracking issue resolution. At a minimum, this specification addresses design review schedule, data transfer protocols, 3D modeling guidelines, model freeze points, component prioritization, model synchronization log, collaboration partner roles and responsibilities, interference report format and content, 4D model specification, required BIM technology, and BIM ownership.
Leave a Reply
You must be logged in to post a comment.